What’s the difference between hot cast and cold cast sculptures?
A hot cast bronze sculpture is built to last. Using ancient techniques, that have survived for thousands of years, it’s an investment that will last generations…
One question we’re often asked by those enquiring about our work—is what the main differences are between cold cast and hot cast bronze garden sculptures. With the significant price step-up involved with choosing hot cast, it’s a perfectly reasonable concern.
Just where does that extra investment go?
Perhaps, understandably, the confusion lies when customers see photographs of our sculptures, and, visually, the differences seem very subtle.
The answer rests in the processes we use to create each individual piece and, as a result, the physical properties that the two types of sculptures inherit.
It’s worth noting that the initial stage of each process is essentially the same—in that we study the original literary illustrations and create clay models with the help of wire skeleton armatures to establish the sculpture’s intricate 3D form.
When that model is shaped exactly how we want it, when every detail of the character is just right, we make a rubber mold—into which we pour two different types of casting: either hot cast or cold cast.
So, with the story set, let us guide you on a captivating journey into the world of hot cast and cold cast sculptures, the processes involved, and how both methods have their own unique characteristics to make a stunning, literary-inspired garden feature.
Hot Cast Bronze
A history…
Hot cast has a fascinating history that goes back for 1000s of years and can be found in a variety of different cultures throughout the ages—from the bronze vessels of the Shang dynasty in Ancient China, to the elaborately-decorated cast plaques from the 16th century West African Kingdom of Benin.
The Cire-Perdue lost wax technique used by the Robert James Workshop—where the wax figure is created from the mold and made ready for bronze casting—has been around for at least 3000 years.
An ancient technique…built to last
Perhaps the most valuable characteristic of a hot cast bronze sculpture is its sheer robustness. The handy thing for us as creators is that there are thousands of years of evidence to prove it.
In the late-1920s, the Artemision Bronze, often known as the God from the Sea, was dragged from the depths of Cape Artemision in northern Greece in near-immaculate condition. The sculpture was made, using ancient hot casting techniques, as early as 450BC. Empires can rise and fall, but bronze will survive.
Indeed, when you buy a hot cast sculpture, water feature or miniature from the Robert James Workshop—you’re investing in a sense of permanence. A garden feature that will last for generations.
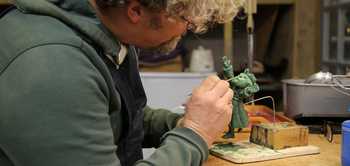
One-off pieces
Another marvelous feature exclusive to hot cast bronze is the chance it affords us to create bespoke editions. In the past, we’ve taken the much-lovedAlice in Wonderland sculpture and produced portraits of customers’ grandchildren and children and transposed them onto the original work.
There's a huge opportunity to be much more creative with the hot cast pieces as we can manipulate the wax before the bronze goes into the furnace. Whether it’s changing faces, or reorienting certain aspects to create a truly unique piece.
Instead of a standard edition sculpture, you’re getting a genuine master.
Colouration and polishing
To achieve the stunning colour effect on our hot cast sculptures, we use a patination process that involves exposure to intense heat. Once the work is cleaned up, and all the seams and textures are precisely how we want them, the golden sculpture is passed over with a gas torch until it's almost cherry red.
We then apply a range of acids and alkalis to the surface which oxidises—just like water does on ferrous metals to create rust. But, instead of orange, with bronze and the introduction of acids and alkalis, you’re treated to a whole kaleidoscope of colours and tones.
It’s also possible for us to polish and highlight certain areas on the bronze to create dazzling mirror finishes. This is remarkably effective for things like buttons, broderie anglaise and edges—any surface features that we want to catch and reflect light. This allows us to create wonderful contrast within our work; a beautiful assortment of colours, textures and finishes which really adds to the visual depth of the piece.
With cold cast, this approach just isn’t possible. If we were to apply that level of heat to the polyester resin, it would simply melt. While we can get a fairly reflective surface with cold cast, it doesn’t have the same visual impact as a golden bronze mirror finish.

Cold Cast Bronze
Treat with care
While you can be confident that a hot cast bronze sculpture will last through multiple generations—in contrast, the cold cast alternative is very much for this lifetime. Kinder on the pocket, but a purchase that needs to be treated with care and a degree of thoughtfulness.
That’s not to say a cold cast sculpture doesn’t have any powers of resilience —after all, it’s used in the creation of large fiberglass boats—just that it will not withstand the same kind of heavy impact of its hot cast equivalent.
So, as a customer, you've got to be considerate about where you position your cold cast sculpture; find a place where there’s no chance of it toppling over, or finding itself in the flight path of a stray cricket ball. Unlike the hot cast version, if a cold cast sculpture receives a hefty whack, unfortunately, it’s going to shatter.
It’s also important to factor in the changing weather over the course of a year, and think somewhat about the measures you can take to protect your sculpture against the elements—something we’re always happy to offer advice on.
The process
Very much a 20th century invention, the cold cast process involves mixing four-parts bronze metal powder, and one part resin. We then put that compound into the mold cold—so there's no heat involved—with glass fiber for additional strength. We then introduce colour with various waxes and mild acids.
Although some degree of heat is created through the chemical reaction involved—at its core, it's an entirely cold cast process. Where needed, we can incorporate stainless steel elements to support the overall integrity of the sculpture. The mixture of bronze metal powder and the polyester resin gives it that near-genuine bronze aesthetic…almost just like the real thing.
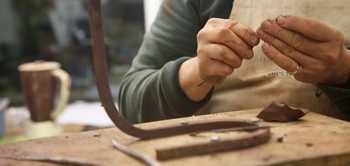
How can we help?
So there we have it. We hope that goes some way to explain the differences between the two processes, and gives you some insight into the price scale of our handcrafted sculptures.
Whichever option you choose, either hot cast bronze or cold, investing in a Robert James Workshop sculpture will mean every step in your garden will be like immersing yourself in the pages of your favourite book. Your outdoor space will become a love letter to classic children’s literature and all the wonderfully memorable characters that inhabit it.
If you’d like any further guidance on the hot cast and cold cast bronze process or would like some advice on maintenance or cleaning your garden sculptures, please don’t hesitate to get in touch.
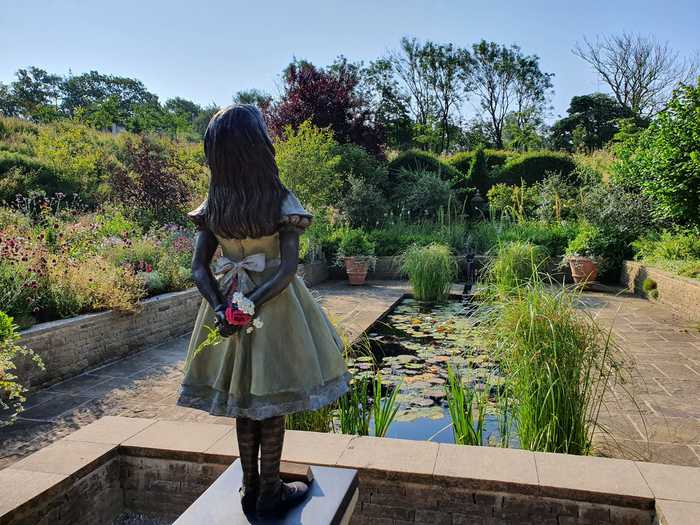
Posted on February 9th 2022